一台机械臂在汽车工厂的焊接车间精准地重复着0.1毫米级的动作,温度传感器实时调整着食品厂的灭菌参数,远在三千公里外的工程师通过AR眼镜指导现场设备调试——这些场景不再是科幻电影的特效,而是中国制造业每天发生的真实变革。工业自动化技术正以前所未有的速度重塑着生产逻辑,其影响力早已突破工厂围墙,悄然改变着每个人手中商品的诞生方式。
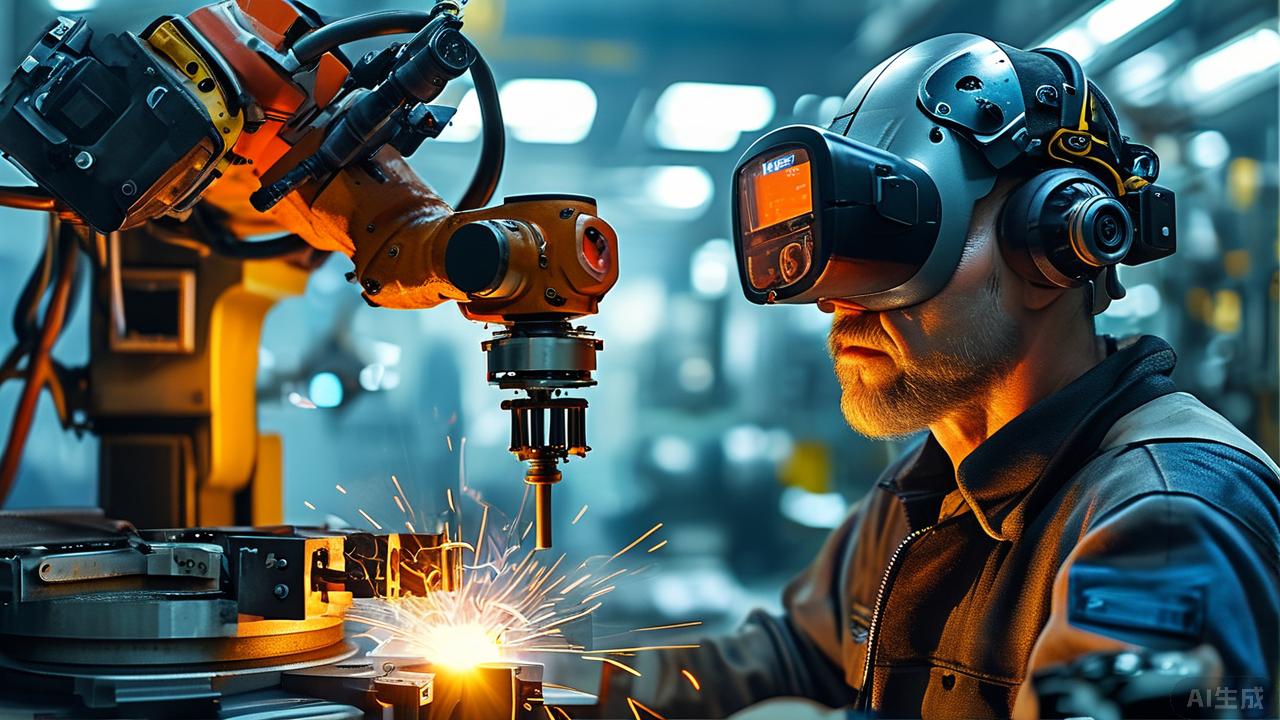
在浙江某新能源汽车工厂的总装车间,当视觉定位系统引导机械手将电池组误差控制在发丝直径范围内时,工位上的老师傅会掏出手机记录这些"新同事"的工作状态。这个充满反差感的画面,恰好揭示了自动化技术演进的关键逻辑:不是替代人力,而是将人类从重复劳动中解放,转而投入更具创造性的领域。就像二十年前数控机床让"八级钳工"转型为编程专家,今天的协作机器人正在培养新一代的"人机交互工程师"。
控制系统的进化史堪称一部微观的工业革命史。从气动控制到PLC(可编程逻辑控制器),从单机自动化到分布式控制系统(DCS),每次跃迁都伴随着认知范式的突破。如同智能手机整合了通讯、娱乐、支付功能,现代工业物联网平台正在将设备监控、能耗管理、质量追溯等模块融为有机整体。山东某化工厂的中央控制室里,操作员面前的大屏实时跳动着两万个监测点的数据流,AI算法在海量信息中捕捉着设备亚健康状态的蛛丝马迹。
在这个由传感器、执行器、控制器构成的数字生态中,每个组件都扮演着独特角色。温度传感器如同设备的末梢神经,激光测距仪堪比精密尺规,伺服电机则充当着灵活的手腕。当苏州某精密制造企业引入自适应控制系统后,其数控机床能在刀具磨损0.003毫米时自动补偿参数,这种微观层面的动态平衡,恰似人体在运动时无意识调节肌肉张力的精妙机制。
工业现场最动人的场景往往藏在细节里。广东某家电企业的质检线上,高速工业相机以每秒200帧的速度捕捉产品外观,深度学习算法在0.8秒内完成32项缺陷检测,这套系统初期训练时"吃"掉了三十万张瑕疵样本图。而在西北某光伏电站,清洁机器人顶着风沙攀爬光伏板时,其路径规划算法会参考气象卫星传来的沙尘移动模型。这些技术细节堆砌出的不仅是效率,更是一种全新的生产哲学——让机器具备环境感知与自主决策能力。
当重庆某车企的焊装车间实现98%自动化率时,人们更应关注那2%的人工介入环节:工程师需要教会机器人识别十三种钣金件变形模式,就像老师傅传授看火候的诀窍。这种人与机器的知识传递,催生出"数字孪生"技术——在虚拟空间克隆出完整的生产线,任何工艺改进都可先进行上万次数字仿真。沈阳某机床厂的经验表明,这种虚实融合的调试方式使新产品研发周期缩短了40%。
站在智能制造的临界点上,工业自动化正在突破物理边界的限制。上海某装备制造企业的远程运维系统能同时监控分布在全球的六千台设备,当莫斯科郊外的机组出现振动异常时,青岛的技术专家通过5G回传的频谱分析数据,在增强现实界面标注出故障轴承位置。这种跨越时空的协同,重新定义了"车间"的概念——控制室的边界正在消融,工业生产进入"云边端"协同的新纪元。
在东莞某电子厂的智能化转型中,最受欢迎的改造不是价值千万的机器人产线,而是一套自动送料系统。当AGV小车沿着磁条轨道将物料准时送达每个工位时,操作员王师傅感慨:"以前每天走两万步搬零件,现在能专心调试设备了。"这个细节提醒我们:真正的技术革新不在于设备的炫酷程度,而在于它是否创造了新的价值维度——或是提升品质稳定性,或是释放人力潜能,或是打开未知的可能性空间。
工业自动化的发展轨迹揭示了一个本质规律:技术进步从来不是目的,而是解决问题的手段。就像蒸汽机终结了马车时代不是因为机械之美,而是它重构了人类对动力的认知。当今天的工程师在调试视觉识别算法时,他们延续的正是这种务实创新的基因——用钢铁与代码构筑更高效、更灵活、更可持续的制造体系,让每个螺丝的拧紧力度都承载着对完美的不懈追求。